当代汽车包含近 1,000 个 IC,它们必须在车辆的全体生命周期(15 年)内运行。这推动了更高的质量期望。虽然 10 Dppm 曾经是一个可靠的基准,但现在是 10 Dppb(10 ppm = 10,000 ppb)。这种变革正在推动巨大的工程研发事情,以筛选细微的测试逃逸并肃清更多潜在的可靠性故障。
在过去五年中,产品工程师和检测设备供应商都开拓了新的测试方法和检测能力,帮助实现 10 毛病 Dppb 目标。这些办理方案办理了半导体器件和组件故障机制。(本文仅关注半导体器件毛病。)
所有这些都须要在汽车行业利用的不同半导体工艺的背景下进行设置。很大一部分汽车 IC 是仿照或稠浊旗子暗记组件,它们采取成熟的技能制造,并且具有更大的最小特色尺寸。用于汽车的成熟技能已经知足 10 Dppm 的目标已有相称一段韶光了,其 ASP 明显低于以 22 纳米及更小节点开拓的繁芜 SoC。从 10 Dppm 升级到 10 Dppb 是一项重大的工程本钱寻衅。
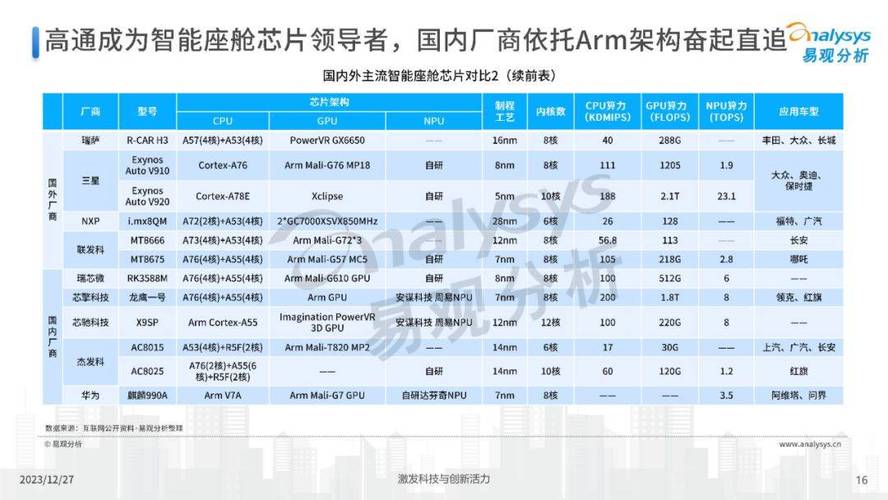
Synopsys数字设计部门的产品营销经理 Guy Cortez 说:“无法承受任何测试逃逸的质量敏感客户将乐意捐躯良率,以确保只向终极客户供应最高质量的设备。” “汽车、医疗和数据中央是质量仍旧非常主要的几个垂直领域。”
由于启用ADAS功能以及处理越来越多的电子传感器的打算需求,汽车制造商现在须要采取前辈 CMOS 工艺的大型 SoC。
产品营销高等总监 Nir Sever 表示:“当前辈节点半导体创造自己正在驱动任务和做事关键型运用时,质量和可靠性变得更加主要,对停机韶光和故障零容忍,例如在数据中央和汽车领域。”在proteanTecs。
高等节点 SoC 包含数亿个晶体管,并包括数十亿个连接多晶硅到金属和金属到金属层的通孔。
PDF Solutions的首席技能官 Andrzej Strojwas 说:“所有这些通孔不仅仅是每个晶圆的十亿分之几。 ” “你现在真的须要用当前的芯片评估十亿分之几。如果要利用晶圆级检测,则干系数字为 ppb 或 ppb 的分数。利用光学设备,您无法包袱检讨每个晶圆层的用度。此外,对付很多现在干系的毛病,它们都被掩埋了。你不能用光学看到它们。”
这种高期望哀求工厂对汽车零部件的检讨和测试操作不断创新。与往常一样,为了减少逃逸,工程师首先转向模具和单元级制造测试。添加新的测试模式可以筛选客户退货。对付可靠性故障,运用高压应力测试肃清了对昂贵的老化过程的须要。
新的逻辑单元故障模型
在 2021 年国际测试会议论文中,恩智浦汽车工程师分享了他们的新测试模式,以筛查细微的全速毛病。一项对汽车客户退货的调查确定了物理根本缘故原由是 PMOS 源极触点短缺其硅化物薄膜,这增加了电阻并影响了栅极延迟。这种行为没有被任何现有的数字延迟故障模型筛选。不幸的是,这种细微的毛病行为从未被不雅观察到,由于现有的ATPG运用故障模型假设单输入开关。
“举例解释这个问题的一个例子可能是两个输入 XOR/XNOR 门,如果两个输入同时改变,它们可能不会在输出端产生逻辑转换。然而,在存在延迟毛病的情形下,输出端可能会涌现延迟转换,这可能会导致时序违规,从而导致故障,”作者阐明说。“为了天生能够暴露此毛病的测试,我们须要有一个针对输入同时转换的刺激。在其他门中可以不雅观察到相同的测试质量差距。尤其值得把稳的是,在较小的几何形状中,米勒电容占主导地位,这会导致输入到输出之间的延迟差异,而其他输入静态与其他输入同时切换。”
通过创建新的故障模型,即多过渡故障模型 (MTFM),并确定运用该模型的高风险标准单元,工程团队为汽车 IC 支配了新模式。一年多来,该团队报告了两种采取 MTFM 模式的大批量汽车设计的生产测试结果。大约 900 万个零件的独特放射性尘埃被丈量为大约 5 Dppm 或 5,000 Dppb。
finFET 的高压应力
工程师连续利用测试来筛选可能对电路可靠性产生不利影响的潜在毛病。潜在毛病可能以部分金属线、金属纵梁或栅极氧化物针孔的形式存在。虽然封装管芯的老化应力会加速这些毛病以表现出故障行为,但对付汽车 IC,可以通过采取晶圆级电应力来跳过这个昂贵的制造步骤。
图 1:致命毛病和潜在毛病的示例。资料来源:KLA
高压应力测试 (HVST) 可加速潜在毛病,然后通过生产测试对其进行检测。可靠性工程师建议利用内部节点切换其状态的动态电压应力 (DVS),以及内部节点保持相同值的增强电压应力 (EVS)。
将 finFET CMOS 器件引入汽车 IC 对运用 HVST 的工程师提出了新的良率/质量/本钱三角寻衅。在 ITC论文等分享他们的办理方案时,恩智浦汽车工艺工程师指出:“随着基于 finFET 技能的产品设计的引入,基本器件物理特性……对高压应力条件下的静态泄露花费有重大贡献。这暴露了如何在 finFET 技能上有效且高效地实行 HVST 的独特寻衅。”
这些寻衅包括:
在升高的电压下不雅观察每个裸片静态泄露的高度可变性,在晶圆探测期间保持 8X 到 32X 的平行度;
无意中触发 ATE 电流钳限定,以及
平衡过低电压应力对产品质量的影响与过高电压应力对产品良率的影响。
作为回应,工程团队根据 IDD 静态泄露丈量对两种不同的 EVS 限定运用了创新的自适应测试方法。他们写道:“它根据实时电流丈量动态调度 HVST 应力电压,以确保每个部件在测试仪硬件电流限定内的最高可能电压下可靠地受到应力,并具有等效的外部毛病覆盖率。” “通过这种办法,它可以实现预期的测试本钱、产品利润和硬件预算,而不会危及产品质量。”
通过对特定工艺节点的表征,工艺可靠性工程师达到了两个 EVS 限定。确定静态 IDD 泄电流限值须要基于产品表征方法。工程团队在 NXP 16nm finFET 产品上评估了他们的 HVST 方法,并报告说在 HVST 期间没有发生电流钳位。
晶圆检测
在制造过程中对关键层进行 100% 晶圆检测的关键驱出发分之一是须要达到足够的质量。只有高速检测系统才能知足工厂中如此高的生产率目标。基于光学和 E-probe 的系统都使汽车 IC 供应商能够识别可能无法通过电气测试的细微毛病。
明场和暗场曝光形式的光学检测仍旧是最常用的生产检测技能。每个都有其优点。明场检测善于检测构造之间的平面毛病或沟槽内毛病,而暗场检测善于检测构造顶部的散射毛病。
KLA 工程师分别与 OnSemi 和 NXP 工程师互助,探索如何利用汽车 IC 零件的检测数据来识别可靠性故障。这些互助推动了非常值检测技能在检测数据中的运用。工程团队最初在 2019 年汽车电子委员会可靠性研讨会上报告了他们的试点研究。在 2020 SPIE论文中,KLA 工程师描述了非常值检测方法,即在线毛病零件均匀测试 (I-PAT),并总结了试点研究结果。
“就其本身而言,过程掌握方法无法决定单个模具是否康健,” KLA计策互助高等总监 Jay Thatter 说。“但 I-PAT 高速检讨筛选的涌现正在创造一个拐点,由前辈的打算能力、图像处理算法和机器学习供应支持。利用 I-PAT 进行筛选会检讨几个可靠性关键层上 100% 的裸片和 100% 的晶圆。将非常值识别方法引入毛病域,现在可以将每个芯片的毛病与更大的总体进行比较,以量化其相对可靠性风险。”
图 2:制造掌握、检讨屏幕和电气测试流程。资料来源:KLA
NXP/KLA 可行性研究利用了来自大约 250,000 个芯片(600 个晶圆,每个晶圆大约有 400 个芯片)的历史数据,他们将 I-PAT 毛病分数与电气测试干系联,包括分类良率、芯片仓、参数值和老化后失落败。I-PAT 分数的阈值可以运用于每个裸片毛病的静态或动态评估。I-PAT 和晶圆测试结果比较的结果表明,有一定百分比的晶圆故障芯片将无法通过 I-PAT 阈值。I-PAT 毛病评分还确定了一些独特的芯片,这些代表潜在的测试逃逸或潜在的可靠性故障。
为了只管即便减少失落败的良模(别号过度杀伤),OnSemi/KLA 团队描述了他们如何在 I-PAT 剖析之前将两个数据过滤器运用于毛病数据。第一个过滤器仅识别设计关键区域中的毛病(毛病敏感性的物理布局剖析)。第二个过滤器利用检测层,个中检测到毛病并通过检测模式(暗场/光场)曝光确定尺寸。结合起来,这两个过滤器将过度杀伤减少了 90%。过滤后,数据通过 I-PAT 方法运行,KLA SPIE 作者描述如下:
“I-PAT 方法利用前辈的干系引擎根据毛病检讨属性对毛病概率进行加权……检讨属性包括毛病大小、位置、极性、检测通道、集群等。该方法调用智能和自适应机器学习 (ML)模型为每个毛病分配一个准确的分类。然后根据毛病对设备可靠性的影响对毛病进行加权。最主要的是对地面实况指标进行适当评估,以验证分类和权重。然后汇总所有缺陷的影响,以供应每个芯片的总体毛病分数。然后利用类似于电气测试筛选中利用的 PAT 方法的统计非常值方法过滤这些芯片级毛病分数。”
图 3:I-PAT 方法组件。资料来源:KLA
通过 SEM 成像,OnSemi 工程师验证 I-PAT 识别出独特的芯片包含潜在毛病。
探测埋孔毛病
电子束供应不同于光学的丈量能力。特殊是,电压比拟使工程师能够检测触点和通孔中存在的亚表面毛病。PDF Solutions 已调度电子束探针系统,以利用专注于有问题的布局构造的矢量扫描模式实行电压比拟度丈量。
“如果您查看 E-probe 工具本身,我们将其构建为矢量扫描仪的主要缘故原由之一是我们将整体 DirectScan 方法与布局剖析联系起来。您基本上可以利用风险最高的模式或诊断工具将模式识别为出错的模式来获取关键层,”PDF Solutions 领先的副总裁 PK Mozumder 说。“你可以运行矢量扫描仪来达到这些点,基本上在两个小时内你就可以得到 ppb 级的分辨率。因此,现在它成为一种制造工具,您可以在生产中利用它来有效地进行非毁坏性处置。”
识别要探测的有风险的布局模式须要在创建掩模组之提高行预事情。确定设计的有问题的布局构造可为检讨设计 (DFI) 添补单元的设计和布局供应信息。这些被放置在非常靠近实际设计的单元布局的地方,利用单元之间的空缺空间。电子束系统对 DFI 添补单元中的金属垫进行丈量。因此,一个产品晶圆可以有数十亿个 DFI 添补单元,是日然供应了十亿分之一的丈量分辨率。
图 4:将易受攻击的布局模式与 DFI 的 E-probe 扫描联系起来。资料来源:PDF 办理方案
然后可以利用电子束探头丈量来识别空隙、短路和潜在的可靠性毛病。在 NANOTS 2021论文中,PDF Solutions 工程师描述了这种丈量能力:
“当用于开路故障模式的 DFI 添补单元垫变暗时,会检测到开路。当不存在毛病时,由于存在接地路径时发射的二次电子,焊盘将变亮。当 DFI Fill 电池垫变亮时检测到短路。DFI 系统能够丈量与软短路或泄露电流相对应的“灰度”级别——我们将其称为 DFI 电气相应指数 (ERI)。为了将灰度级校准到泄电幅度,将 DFI 测试构造放置在划线中,以便在同一测试构造上丈量泄电和 DFI ERI。”
图 5:利用电压比拟暗图像的电子束探头表示开路。资料来源:PDF 办理方案
将灰色单元包含在从坏到好芯片的黑白单元之间的能力为工程师供应了下一个制造测试步骤的选择。此外,该电子束丈量数据补充了电气测试数据,可检测个中一些软毛病。泄露量大的将无法通过电气测试,而泄露量小的则无法通过电气测试,终极可能会在现场失落败。
“只管如此,您仍旧希望从测试数据中受益,由于这样您就知道除了测试中弹出的旗子暗记之外,您还得到了哪些旗子暗记。PDF Solutions 的可制造性设计总经理 Marcin Strojwas 说,您的测试署名中会涌现一些漏洞。“然后,仅仅由于这些泄露的性子,将会有一些略低于你在零韶光在测试中能够检测到的阈值。”
将晶圆检测与测试数据相结合
在过去十年中,工程师一贯在以新的组合办法利用不同的数据源来实行根本缘故原由的良率偏差,同时通过更早地识别质量问题来优化晶圆、组装和测试工厂的运营。检测数据——光学、插值晶圆图、电子束——可以与电子筛查相结合,以识别潜在的测试逃逸和与可靠性干系的故障(潜在毛病)。
“如今,整合这些不同数据源的一个关键驱动力是努力阻挡低可靠性设备逃逸到汽车供应链中,在这些供应链中可能会发生关键任务或安全关键故障。业界众所周知,测试无法识别和阻挡每个坏芯片,因此纵然测试覆盖率极高,也会发生逃逸,”KLA 的拉特说。“当汽车制造商利用来悛改发布节点的设备时,产量较低,问题会变得更糟。并且这种逃逸的统计可能性比指定的期望的十亿分之一哀求赶过几个数量级。须要新的方法来确定哪些模具适宜用场。”
划痕检测,从宏不雅观到微不雅观毛病
晶圆上的划痕可能会导致芯片级可靠性故障。通过结合晶圆测试数据和特定层的 100% 晶圆检测,工程师可以增加对划痕的检测。在 2021 年前辈半导系统编制造会议论文中,来自 SkyWater Technology Foundry 和 Onto Innovation 的工程团队描述了他们对晶圆划痕检测的关注:
“由于划痕图案独特且对付准确检测至关主要,我们意识到我们须要超越 SPR Engine 供应的标准划痕检测算法。因此,我们构建了一个额外的后处理算法,专门用于运行基于图像的划痕检测,而不是利用动态阈值确定(基于密度和分布)的基于毛病的检测,以肃清或减少误报。”
图 6:基于图像的晶圆划痕检测建立在基于毛病的检测之上。资料来源:创新
识别划痕导致识别潜在的可靠性故障。带有划痕的裸片或其相邻裸片可能会通过晶圆测试,但可能会在单元级测试或现场测试中失落败。这是为什么?
“从物理上讲,晶圆划痕可以是密集的,也可以是薄的。它们可以指示微裂纹。并且由于晶片切割时的材料物理特性,这种划痕/裂纹将扩散到受影响的管芯边缘和/或相邻管芯。那些相邻的芯片代表了可靠性故障,” Onto Innovation发卖和客户办理方案总监 Prasad Bachiraju 说。“特殊是在汽车领域,当他们检测到这些类型的故障 [SiC 划痕] 时,他们不想冒任何风险。以是它们会在间隔划痕不到两毫米的地方去世掉。”
成熟稠浊旗子暗记 IC 的潜在毛病
稠浊旗子暗记/仿照设备主导着汽车电子掌握单元 (ECU),它们是在非常成熟的半导体工艺上制造的。然而,这些 IC 供应商也须要将质量目标从 10 Dppm 提高到 10 Dppb。在 2020 年欧洲测试研讨会论文中,OnSemi 工程师和 Katholic 大学的研究职员探索了将模具检测数据与每个模具电气测试数据相结合,以增强动态零件均匀测试。称为视觉增强 DPAT (VE-DPAT),他们的目标是筛选出动态 PAT 未检测到的细微潜在毛病,险些没有产量丢失。
工程团队研究了将两个数据源与乘法相结合。他们将其描述为新的指标。
“筛选参数 α A,D i被布局为两个标准化数的乘积,并作为结果给出一个标准化数。选择这种配方是由于它具有优胜的性能。它可以用于不同的规格,从以纳安表示的泄露丈量到以 MHz 表示的振荡频率。这两个标准化数字的一样平常阐明险些可以被认为是有缺陷设备的概率。”
其他方面的标准化值,非常值检测率显著提高,并且在生产测试过程中更易于履行。
关于通过/失落败限定,他们写道:“在打算丈量 A的筛选参数 α A,D i之后,如果值 α A ,D i超过由设计。在实践中,模具 D i被授予一系列非常值参数 α A,D i,即针对创造毛病的每一层,结合激活非常值方法的每个丈量值。”
直接的乘法可能会导致具有不干系电气偏差的毛病,从而导致不必要的良率丢失。为了改进乘法,他们利用了设计工程师对布局、毛病大小和电气测试的潜在干系性的理解。
OnSemi/KU 团队评估了采取 0.35µm 双极 CMOS DMOS (BCD) 技能制造的升压双降压 LED 驱动器(用于 60V 和 1.6 安培的汽车照明运用)的 VE-DPAT 指标。数据是从 5 个批次的 25 个晶圆中网络的,数据包括 7 个晶圆制造步骤的检讨和每个芯片约 400 次电气测试。在将第一种乘法方法运用于各种检测阈值时,他们报告说,当 TH 即是 4 时,额外的 1% 谢绝,当 TH 即是 10 时,谢绝了 0.1%。与同一 DMOS 上的非常电流泄露干系的输出驱动器的 DMOS。”
结论
工程团队在知足汽车制造商极其严格的 10 Dppb 质量目标方面取得了长足的进步。工程师选择支配的方法将对应于半导体技能成熟度和产品的 ASP。随着车辆中创造的广泛的半导体技能,人们可以期待广泛的办理方案。工程师必须同时找出细微的毛病,同时保持最小的本钱——以美分和 0.01% 的良率丢失来衡量。由于在汽车行业,虽然质量至关主要,但保持供应商盈利能力也是如此。--Anne Meixner