通过对 CMOS 芯片引线键合过程中发生铝焊剥削落和涌现“弹坑”两种征象进行剖析,明确了该类故障征象的发生是由于键合焊盘受到了不同程度的机器浸染而产生的不同程度的损伤。对可能造成该类故障征象的成分进行剖析,紧张成分有:芯片自身存在构造薄弱或原始毛病,键合股料、键合参数等匹配不佳,操作中引入的不当成分等。对引线键合的办法和原材料进行优化,选定自动金球键合工艺,并采取单一变量法和正交优化法对自动金球键合的工艺参数进行优化,给出了自动金球键合工艺参数优选范围。通过环境试验对 CMOS 芯片自动金球键合工艺进行了可靠性评价。
弁言
在微电子组装中,引线键互助为一门繁芜的组装和制造工艺技能,是提高通用微电子器件、专用集成电路、薄厚膜稠浊集成电路、多芯片组装、系统集成电路等微电子电路性能的关键技能,是实现微电子互连的核心技能。无论在传统封装还是前辈封装领域中,芯片引线键合技能都是核心技能。CMOS 芯片引线键合在微电子互连中是普遍的紧张形式。引线键合工艺的研究很多,但紧张集中于键合工艺方法的研究和工艺参数的优化,对键合过程中失落效的研究较少。在键合过程中,键合焊盘受不同成分的影响涌现了不同程度的机器损伤,表示出了不同的故障征象,一样平常有键合焊剥削落和“弹坑”两种征象,该问题在生产过程中涌现的较为普遍,会造成产品的系列返工,对生产的稳定性和产品的可靠性都有着很大的影响。
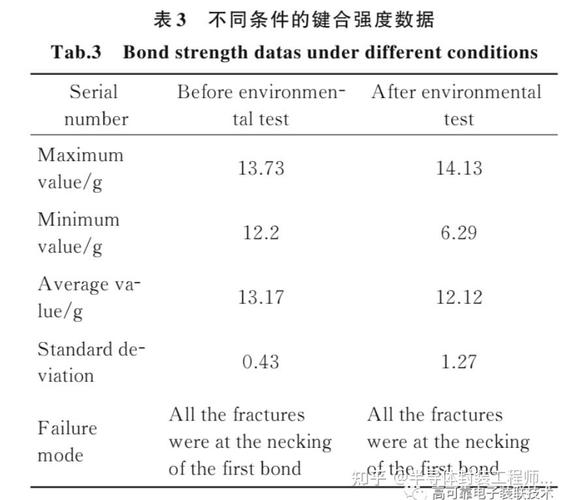
本文基于故障征象本身,对产生键合焊剥削落和“弹坑”两种故障征象的影响成分进行剖析,确认各成分对故障征象的影响机理。针对性办理CMOS 芯片在键合过程中失落效问题,并给出有效方法,为CMOS 芯片引线键合技能供应技能支撑和可靠性保障。
1 故障征象剖析
CMOS 芯片在引线键合过程中受到不同程度的机器损伤,涌现了键合焊剥削落和“弹坑”征象。针对两种征象的焊盘损伤程度和残留描述进行逐一剖析。
1.1 键合焊剥削落
键合焊剥削落是指在引线键合过程中焊盘表层金属层涌现了局部的撕裂进而剥落,键合点随之抬起,剥落的金属与引线审察结合,光学显微镜下的失落效描述如图1(a)、(b)所示。
进一步对焊盘失落效点进行SEM 剖析,失落效点边缘有很明显的撕裂痕迹,局部剥落露出绝缘材料(BPSG)层,如图1(c)所示。该类型失落效是表层金属化层和下层绝缘材料之间受机器浸染而产生分离,随后在持续的机器浸染下涌现了焊盘局部撕裂剥落。
1.2键合焊盘涌现“弹坑”
键合焊盘涌现“弹坑”是指在引线键合过程中焊盘局部涌现了一个不固定形状的凹坑,凹坑中有少量硅被挖出,键合点随之抬起,凹坑中被挖出的硅与引线审察结合,光学显微镜下的失落效描述如图2(a)、(b)所示。
进一步对焊盘失落效点进行SEM 剖析,焊盘局部涌现了一个凹坑,个中的硅材料被挖出,如图2(c)所示。该类型失落效是键合焊盘和下层材料受机器浸染而产生微裂纹,后在持续的机器浸染下持续扩展致局部晶体解离,凹坑中的硅材料被挖出,形成一个“弹坑”。
通过以上剖析,得出两类故障征象均为在引线键合过程中焊盘受机器浸染而产生的不同程度的损伤。虽然该类损伤产生的直接缘故原由是机器浸染,但芯片自身毛病、键合工艺参数、键合股料成分、键合操作过程中不明确成分等都是匆匆成其终极发生的成分。
2 故障定位和机理剖析
目前COMS 芯片引线键合常用的办法有铝丝超声键合和金丝热超声键合两种办法。超声键合是一种固态金属结合办法,当超声能量和力被施加到连接工具时,超声波能量浸染的刮擦动作毁坏了键合焊盘上的氧化物,在铝引线和铝焊盘打仗面处产生微塑性变形,因而打仗面机器互锁实现键合。热超声键合则是金原子和铝原子相互扩散及电子共享形成的一个冶金学结合。在热超声键合中,除了压力和温度之外,利用超声波能量使得固定位置的断层被激活和驱动,引起金属软化且相互滑移并发生低应力变形,增强扩散和反应实现键合。超声键合和热超声键合都须要利用键合工具,即劈刀来固定引线,并通过劈刀来通报一定的热能、力和超声能量来实现金属引线和金属焊盘之间的有效键合。
CMOS 芯片在引线键合过程涌现失落效,可能与芯片自身成分、键合干系工具材料、键合过程中引入的能量以及操作等成分干系。根据以上推论,并结合故障描述剖析得出在引线键合过程中可能造成键合焊剥削落和涌现“弹坑”的成分有:硅节瘤的存在、键合焊盘下层材料及金属层厚度、键协力、键合超声波能量、键合工具的类型、引线硬度、工具的冲击速率和冲击力、与操作者干系的不定性成分等等。这些成分之间相互关联,常日是几个成分综合浸染的结果。本文对可能造成该类故障征象的以上成分进行剖析。
2.1 芯片问题
目前所利用的CMOS 芯片是采取CMOS 工艺制作而成,即将NMOS 器件和PMOS 器件同时制作在一个硅衬底上。CMOS 芯片是多层布线,层间采取金属通孔互连,如图3 所示。从芯片自身来剖析,导致键合焊盘露底的干系成分有:硅节瘤、键合焊盘附着力差和键合焊盘镀金层薄。
芯片在制片工艺过程中掌握不得当,会有微米尺寸的硅节瘤沉淀在铝键合焊盘上,在有机器外力施加的时候,这些硅节瘤可以充当应力集中源,使得下面的硅分裂。如果芯片键合焊盘存在硅节瘤,在引线键合过程中的机器浸染下,很随意马虎引起露底,呈“弹坑”征象。故硅节瘤是诱发键合焊盘露底的一个成分。
CMOS 工艺芯片采取多层布线,常日会做到7~8 层布线构造,层与层之间通过金属通孔互连。考虑到基底硅材料会存在硅钉穿孔的征象,故一样平常通孔尺寸小于1 μm(常日为0.6 μm 或者0.8 μm)。由于通孔尺寸极小,故金属焊盘(以100 μm 尺寸焊盘为例)紧张和硅磷玻璃层相结合。比较较而言,GaAs 材料的MMIC 芯片其布线一样平常只有2~3 层,层间互连的金属化通孔尺寸一样平常达到70 μm 旁边,故金属焊盘(以100 μm 焊盘为例)紧张和通孔金属相结合,如图4 所示。由于金属和金属的结合力相对金属和硅磷玻璃的结合力会强很多,故CMOS 芯片的焊盘附着力相对较弱。在引线键合过程中的机器浸染下,其焊盘更随意马虎涌现撕裂剥离,呈焊剥削落征象。故键合焊盘附着力差是诱发键合焊剥削落的一个成分。
键合焊盘金属化层厚度对露底发生的影响紧张是“缓冲效应”。如果焊盘金属化层较厚,对外力有一定的缓冲浸染,同时由于金属的塑性变形也会使机器浸染衰减;如果焊盘金属化层较薄,键合机器浸染下涌现露底的概率也较大。故键合焊盘金属化层薄是诱发焊盘露底的一个成分。
2.2 键合股料问题
引线键合过程中,对焊盘有直接机器浸染的材料紧张是劈刀和引线。
劈刀长度属于振动系统的一部分,当劈刀越长,其尖端摆幅会越大,通报更多超声能量至焊盘。键合劈刀的构造设计如果没有充分考虑,劈刀杆长过长,在产生同样形变的情形下,键合焊盘所承受的机器外力就更大,对焊盘损伤的概率也大。故键合劈刀不匹配是诱发焊盘露底的一个成分。
键合引线的硬度与所需超声能量干系,即超声能量E=K(HT)3/2,个中K 为常数,H 为线硬度(维氏),T 为金属厚度。引线越硬,产生一定形变须要的键合超声波能量就越大,过大的超声波能量会增加键合焊盘发生露底的概率。故键合引线过硬是诱发焊盘露底的一个成分。
2.3 键合参数问题
键合焊盘露底的直接缘故原由是受到机器外力的浸染,故与其直接干系的键协力和键合超声波能量是非常紧张的成分。
键协力过大或过小都易导致露底,力大较易理解,但力小导致露底是劈刀与键合面未紧密接合,产生尖端效应导致。在干系研究中键协力与露底发生率之间有着对应关系。随着键协力的增加露底发生率先减小后增大,在某一个值达到最低点。故键协力不匹配是诱发焊盘露底的一个成分。
键合超声波能量不匹配,会诱发硅中的叠层错位和引起其他材料损伤。当键合工具在键合焊盘上压紧引线时,二者局部的点在实际的物理打仗中。这时当焊盘下面有一个眇小的毛病,超声波能量和局部的高压力将通过微裂纹进行传播,如图5 所示。如果键合超声波能量不匹配,诱发硅中的叠层错位或者引起了其他材料损伤诱发露底。故键合超声波能量不匹配是诱发焊盘露的一个成分。
2.4 键合操作问题
键合操作问题一样平常指键合过程中工具的冲击力和冲击速度过大,而引入非正常的机器外力,造成键合焊盘损伤。除此之外,还有一些不愿定的人为成分引入的滋扰。故操作问题是诱发露底的一个成分。
综上剖析,部分芯片由于自身存在构造薄弱或者原始毛病等问题,导致其后续引线键合的工艺窗口变窄,加之在其键合过程中工艺材料、工艺参数和工艺操作不足优化的情形下,就会涌现焊剥削落或焊盘“弹坑”的失落效。故对CMOS 芯片引线键合工艺进行优化,为其引线键合技能供应技能支撑和可靠性保障。
3 键合工艺优化和可靠性评价
本研究针对以上问题,对引线键合办法、原材料和工艺参数进行优化,给出相应的办理方法。
3.1 键合股料和办法优化
通过以上剖析得知,键合引线过硬是诱发焊盘露底的一个成分,故针对该问题选择硬度较小的引线。按照American Fine Wire 的产品目录供应的键合引线材料的物理性子中供应的数据,Au 引线硬度为220 N/mm(2 布氏),Al 引线的硬度为200~500N/mm(2 布氏)。从引线硬度这一成分来看,针对露底发生率而言金引线相对有一定的上风。本实验研究采取25 μm 金引线键合,同时匹配选择了杆长12 mm、FA(端面角度)8°、OR(外半径)值25.4 mm的劈刀。
金球热超声键合由于其第一焊后可360°自由移动,第二键在任何方向均不损伤球颈,效率高。综合上述剖析结果,本实验研究选择自动金球热超声键合。
3.2 键合参数的优化
根据上述研究选用25 μm 金丝在CMOS 芯上进行自动键合,第二键选定陶瓷基板且参数设置为定值。采取单一变量法研究其紧张的工艺参数超声功率、超声韶光、键合压力对键合质量的影响。根据单一变量法研究的结果,选取参数进行三成分三水平的正交优化试验,给出最优参数选择。
3.2.1 键合参数对键合质量的影响
通过掌握单一变量法分别对超声功率、超声韶光、键合压力进行研究。结合履历值,每个变量选取10 个参数值,每个参数值对应键合200 根丝。对键合金丝的描述、键合强度(100 根)和球剪切强度(100 根)进行测试。通过以上研究得出,在CMOS 芯上进行25μm 金丝键合的优选参数范围如表1 所示。
3.2.2 键合参数的优化
通过3.2.1 的研究结果,选取参数进行三成分三水平的正交优化试验,给出CMOS 芯金丝键合的最优参数选择。试验设计如表2 所示。
按照表2 参数进行三成分三水平的正交优化,共计27 组参数组合。每组参数对应键合200 根丝。对键合金丝的描述、键合强度(100 根)和球剪切强度(100 根)进行测试。在键合和测试过程中均未发生露底征象。根据测试结果得到最优参数组合为(60 mW、30ms、25 g)。
3.3 键合可靠性的评价
按照以上正交试验优化的参数组(60 mW、30ms、25 g)进行键合。键合400 根金丝,分为2 组用于环境试验前后的比拟剖析。结合产品筛选考察的哀求以及实际条件,适当加严确定环境试验条件为:
高温储存:125℃,168 h
温度循环:-55~+125℃,变温率10℃/min,保温15 min,循环20 次
恒定加速度Y1方向,保持1 min,20 000 g
对环境试验前后的键合金丝的描述、键合强度(100 根)和球剪切强度(100 根)进行测试剖析,结果如表3、表4 所示。
键合过程中没有涌现焊盘露底等征象,且键合的可靠性知足了GJB548和产品的筛选哀求。该键合工艺过程稳定、可靠性高,可以知足产品批量化的生产需求。
4 结论
1)通过对CMOS 芯片键合过程中发生的焊剥削落和“弹坑”两种征象进行剖析,明确了该类故障征象是由于键合焊盘受到不同程度的机器浸染而产生的不同程度的损伤。
2)通过剖析得出部分芯片由于自身存在构造薄弱或者原始毛病等问题,导致其后续引线键合的工艺窗口变窄;加之在其键合过程中,工艺材料、工艺参数和工艺操作不足优化,就会涌现焊剥削落或“弹坑”的露底失落效模式。
3)对引线键合的办法和原材料进行优化,选定金引线和热超声键合的办法,同时为了打消键合过程中的操作不当成分,选择了自动金球键合工艺。
4)采取单一变量法和正交优化法对自动金球键合的工艺参数进行优化,给出了自动金球键合工艺参数优选范围。
5)通过环境试验对CMOS 芯片自动金球键合工艺进行了可靠性评价,通过评价确认该键合工艺过程稳定、可靠性高,可以知足产品批量化的生产需求。
本研究的工艺技能和参数可以运用于CMOS芯片引线键合技能的工艺设计和操作辅导。